Wiley Process Engineer, Heath Barker, has a passion for robotics and automation and has been in Munich to attend Automatica 2016. His next stop was the Airbus facility in Germany. We love sharing knowledge from these events with our network to help us all reach peak performance and ensure our global food security into the future.
Following a busy week at Automatica, I had the pleasure of visiting an Airbus Facilities. Hamburg is the headquarters and the largest Airbus site in Germany. The site employs around 12,500 people and plays a key role in the development and manufacturing of all Airbus aircraft. Around half of Airbus’ annual production of A320 family aircraft are assembled, painted, and delivered to customers from all around the world in Hamburg (262 in 2015).
We traveled by bus for 5 minutes (and advised no photography was allowed, sorry folks) passing about 50 office buildings, and a number of massive maintenance buildings and stock warehouses.
During orientation I particularly loved the section on Airbus’ future vision. It made me feel inspired and excited for what the future holds. You can view it on their website.
We were shown a section of wall panel from an A320 with the internal trim removed to expose the wiring, hydraulics and insulation. It was interesting to see how other industries run their services. In terms of quality and aesthetics, I believe the food industry is definitely ahead of the game.
Next we were shown the range of Airbus models. There were about 15 models on a wall displaying various statistics such as weight, carrying capacity and flight range. My favourite models were the A380 and the Beluga. The Beluga is a plane dedicated to carrying really large items, particularly other Airbus bodies – yes, this plane carries planes inside itself! The facility has its own airstrip that allows these large assemblies to be flown in and out. In fact, as we were leaving I saw one take off which was a real treat.
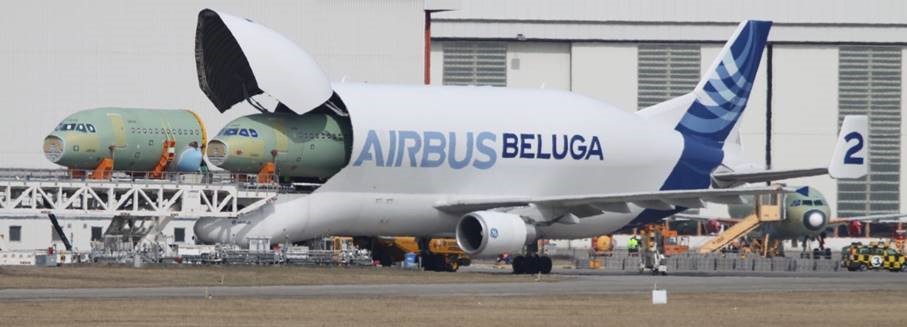
Sourced from Wikipedia
Having completed orientation, we entered a larger building dedicated to the final assembly of A320s. The facility had huge spans with no supports in order to avoid hindering product flow.
We were shown the end section of an A320 with hydrogen fuel cells installed first. This is a prototype with the idea to power the planes electrically as they taxi on the tarmac. This technology saves about half of the fuel used during taxiing and is another step towards a more sustainable industry.
We toured through the A320 wing and tail final assembly area and watched a crew fitting a wing to the body.
Whilst I expected to see more automation, I came to realise that the main focus was on ergonomics for the operators to improve efficiency and quality while reducing health and safety risks.
From the A320 building we traveled to a massive seven story warehouse. Again there were enormous spans without supports to allow the full movement of assemblies unhindered. The Hamburg facility only looks after the fabrication of portions of the body, tail and the doors of the A380. The remaining parts are fabricated in France, Spain and the UK.
A380 parts are moved around in the facility on 30m long, 4m wide flatbed trailers with omnidirectional wheels (the same wheels as on many of the AGVs from Automatica). This allows the platform to travel in all directions and rotations as required.
Similar to the A320 building, there was very little automation throughout the facility. Everything was completed by hand with the assistance of customised mobile scaffold-like structures that surround and support the enormous sections of aircraft as they are fitted out and assembled. These scaffolds huge, up to six stories high and are driven into position then hydraulic arms lock onto the ground and assembly.
Our final stop was a visit to one of the many A380 hangers to see the fully assembled A380s from below and then, after climbing about 10 flights of stairs, from above. In these hangers all of the systems checks are performed before delivering to customers. The size and detail of the wings and jet engines were really something to behold.
Up close this is an amazing feat of engineering and whilst there was very little automation in the form of robotics and machines, the methods used for transporting assemblies and improving operator ergonomics were very impressive and the food industry could learn a thing or two from them.
To discuss your robotics and automation needs further, please contact Heath or Wiley.